companyYamato Intec seen through history
With the history of 430 years, we have been walking with casting field.
【Four turning points】 1: From the founding period to modern times, the production of a wide range of “casters” in Shinano Province
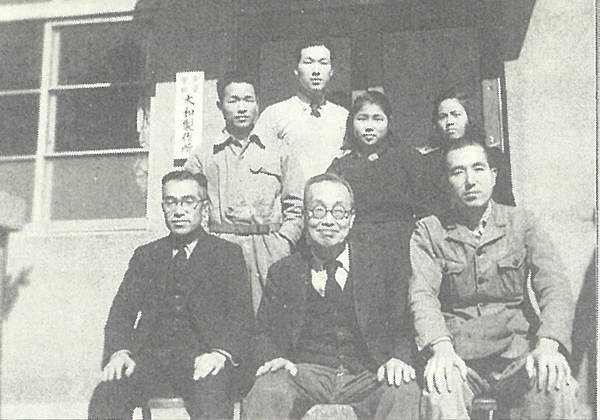
In 1584, Sadayoshi Ogasawara, the lord of Matsumoto, invited the first Hamaiemon Kiyokata to Matsumoto from Yui, Kamakura County, Sagami Province, and founded it near Matsumoto Castle. As an “Imoji” who manufactures weapons and Buddhist altar fittings in Shinano Province, he was later connected with the Shinji family who controlled the Japanese casting world at that time, and was given a “Iwami-cho” of receipt and became an advisor.
It is said that many craftsmen such as foundry makers, nabeya, and stone shops brought by Mr. Ogasawara when he was transferred from Iida and returned to Matsumoto in 1613 in Iida in Iida-cho, Matsumoto City, where the old company building was located until the 1960s.
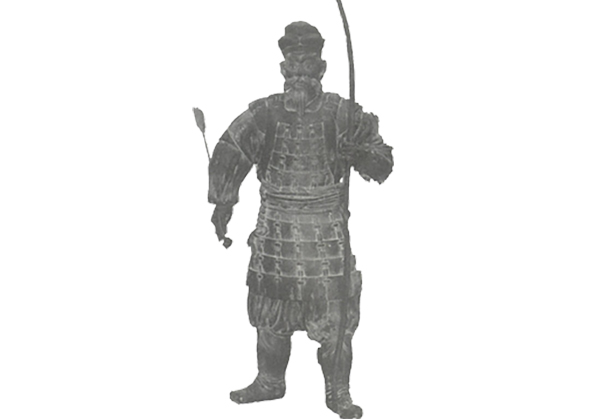
After that, the bell of Ushibushi-dera Temple (Kiyotsuna Saku) in Kataoka, Shiojiri City, and Sumiyoshi Shrine in Misato, Azumino City, where a wooden shape still remains at the entrance of our company, “Sakanoue Tamura Maruro-ko Statue (age scandal)” (derived from the story that exterminated the Eight-faced king, the actual product was provided at the time of the Pacific War), etc. He works on many bells and statues of shrines and temples. Since the Meiji period, it has produced agricultural equipment, daily necessities, silk-making machinery, munitions, etc.
Among the long-established companies that have been in business for more than 100 years commended by the Matsumoto Chamber of and Industry, it is the second longest after the Owariya Somemono Main Store, which was founded in 1575.
- Showa 11 (1936 AD)
- Limited Partnership Hama Iron Works
- Showa 21 (1946 AD)
- Yamato Seisakusho Limited Partnership Company
- Showa 28 (1953 AD)
- Yamato Seisakusho Co., Ltd. was born. In response to the trend of motorization after the war, we mainly manufacture brake drums for motorcycles and tractors.
- Showa 37 (1962 AD)
- Moved to Hirooka, Shiojiri City. Around this time, the manufacturing of exhaust manifolds for small trucks began.
【Four turning points】2: First turning point V process practical application Exterior as the main axis
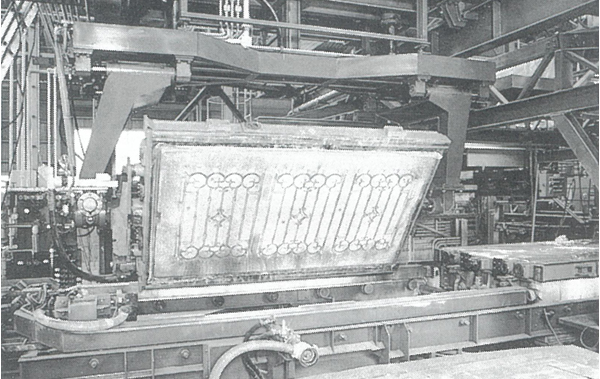
In 1971, the Nagano Prefectural Industrial Experiment Station succeeded in developing the “V-process molding method” (vacuum seal mold process), which later became a world patent. Our company also introduced it from the standpoint of joint development, and it became possible to cast large aluminum products. However, it is forced to struggle due to the undeveloped market and the series of defects due to prototypes.
In 1977, he received the “Okochi Memorial Technology Award” for V-process development, which was honorable in Japan at that time. From here, we took advantage of the expansion of the exterior market and the wave of luxury orientation in the bubble period, and greatly increased our business performance in exterior products, which became our main business.
In 1981, the fastest V-process molding line was invested and installed. It was a forced installation that considered to anticipate the era of the heyday of the exterior by the V process, but as a result, this became a high-power facility with a look ahead.
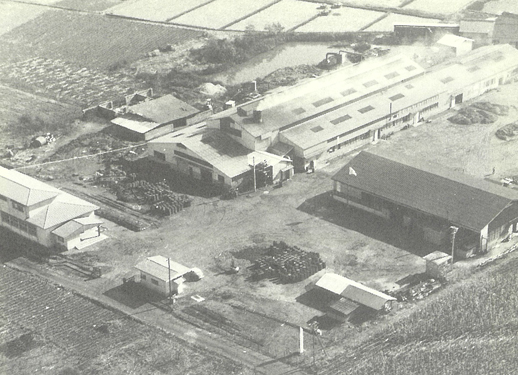
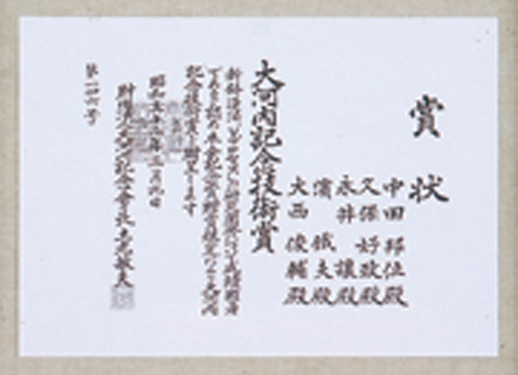
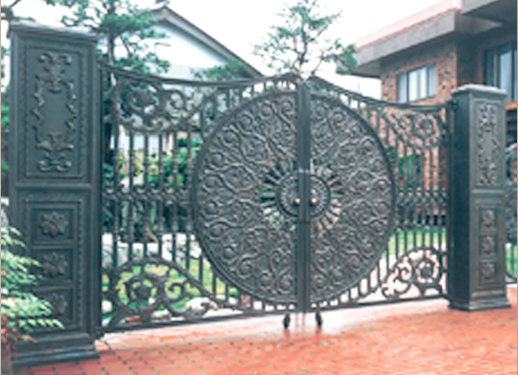
【Four turning points】3: The second turning point, the collapse of the bubble, to specialize in turbochargers
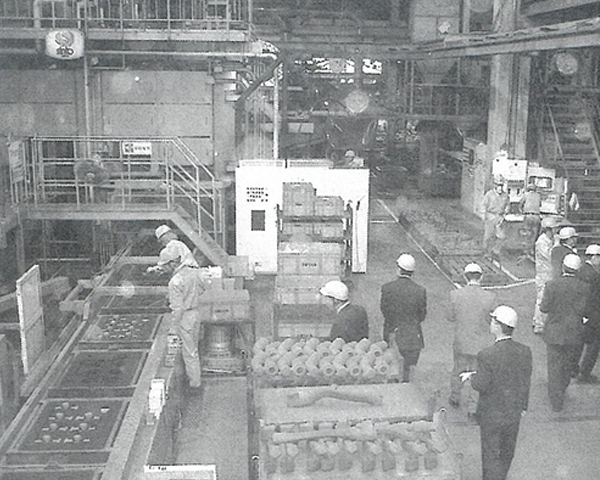
Business performance deteriorated due to the collapse of the bubble economy from the beginning of the Heisei period and the corresponding head of the exterior market. In 1989, with the aim of revitalization of the cast iron division, which was in decline at that time, we started the APK line plan and made a huge investment.
In 1991, the name was changed from Daiwa Manufacturing Co., Ltd. to Yamato Intec Co., Ltd., and the APK line was completed in 1993.
In 1997, we were forced to change our policy due to a large amount of upfront investment and lease repayment.
However, in 1999, we reviewed our specialty and decided to specialize in exhaust manifolds, which used to be our main products, and turbocharger parts as new challenge parts. As a result, we achieved a recovery in business performance.
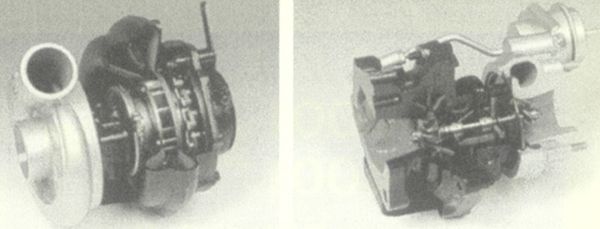
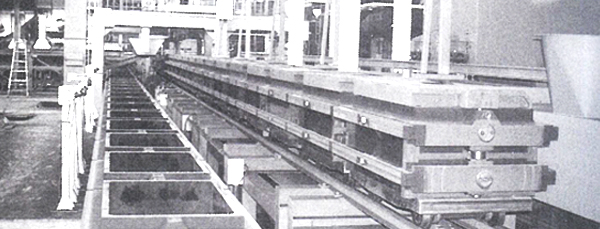
【Four turning points】4: The third turning point, response to multi-products, small quantities, and multi-materials
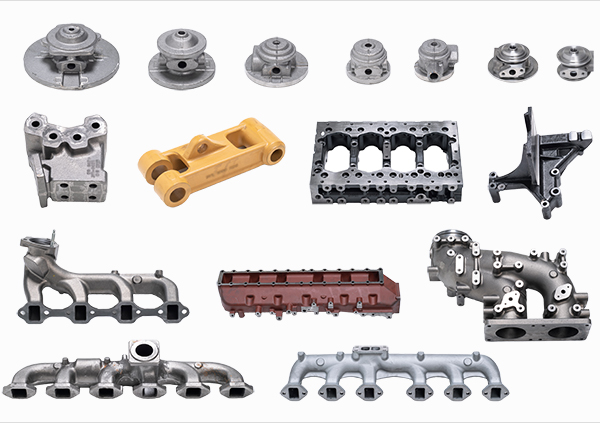
In 2007 (2007), we worked on the adoption of the world’s first power supply system to renew the power supply and improve the capacity of the 3t-2200kw high-frequency induction furnace installed in 1981. After trial and error, it was completed in May 2008. It is a turbocharger part of a diesel engine with advanced environmental measures, and at one time it has grown to 10% of the world’s market share.
In an era where not only casting but also “processing consistency” is required, we responded quickly to the needs with the strengths of many varieties, small quantities and multiple materials while strengthening processing facilities.
【Four turning points】5: The fourth turning point, grasp the future with a view to overseas
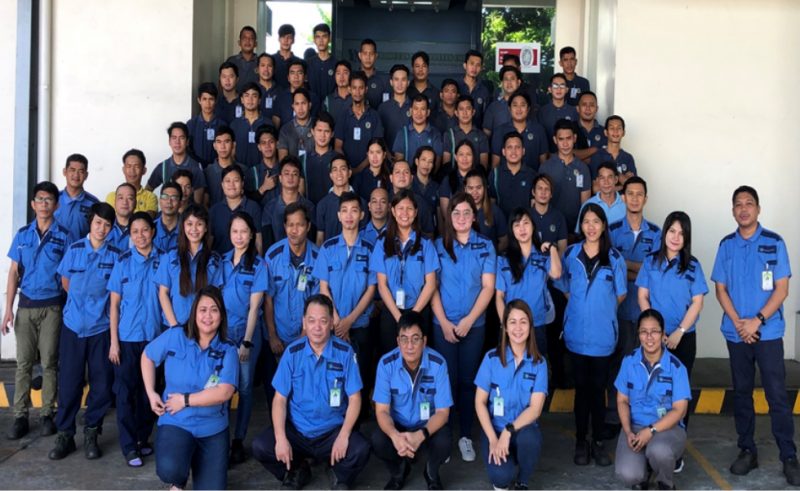
From 2011 to 2012, a manipulator for picking up loose products and a double belt conveyor for transporting sand were introduced from Germany. In 2013, the company rented a factory and relocated production equipment to the Philippines, and began outsourcing part of the bearing housing manufacturing process.
In 2017, we established a joint venture company, YNPC, in the Philippines, and at the same time expanded our production facilities. In 2020, it became an independently owned subsidiary. At the same time, we are also considering collaboration with the Chinese market, and are looking to a new stage as a global, multi-purpose casting manufacturer.